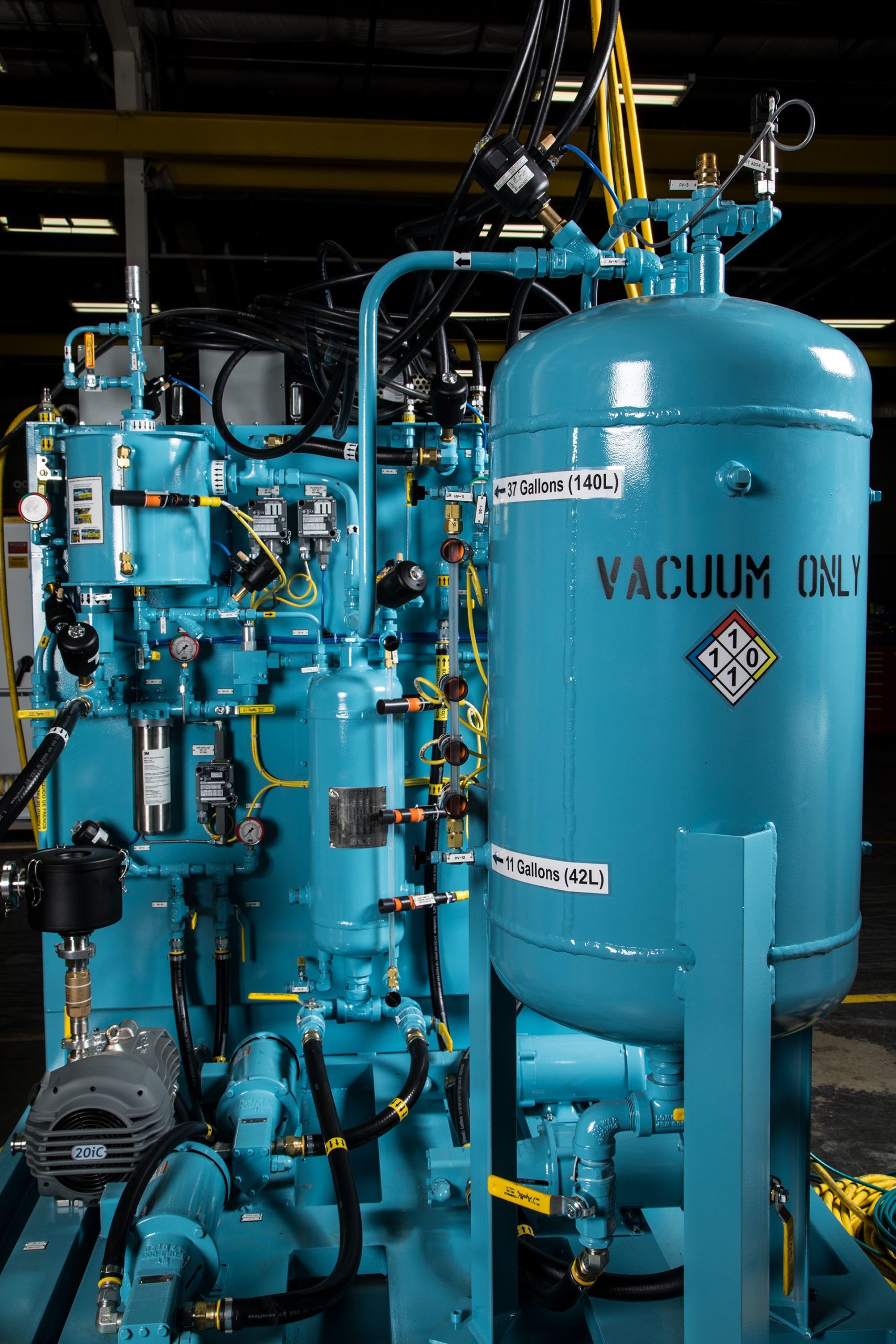
Four Best Practices for Improving the Efficiency of your Refrigeration System
Refrigerant system evacuation may only take a few minutes, but it’s one of the most vital processes in ensuring a quality refrigeration system. Proper refrigerant system evacuation checks for leaks, remove harmful contaminants and increases the efficiency of the system. Yet, it’s a process most manufacturers—especially those manufacturing automobiles and appliances—have not perfected.
Incorrect evacuation is costing manufacturers efficiency ratings. A study by Purdue University’s School of Mechanical Engineering shows that household appliances with 0.5 percent air left in the circuit can have an increase in energy consumption by 10 percent. How significant is removing just 0.5 percent of air? If each of the 126 million households in the U.S. had one refrigerator using 850 kWh per year, the energy savings would be enough to offset an entire nuclear power plant.
Fortunately, proper evacuation is not hard to achieve.
1) Determine the Actual Time Needed to Evacuate
In manufacturing, every process is expected to be completed in a certain amount of time. In general, this makes sense. It ensures production schedules stay on time. The problem is that most companies are having to guess at the maximum time needed to evacuate a refrigeration system properly.
One customer took a product prototype and purposely left it open for two days so moisture could penetrate the refrigeration system. They then hooked the system to the vacuum pump and evacuated the system in ten-minute increments: 10 minutes on, wait for the system to equalize, evacuate for 10 minutes more, wait, and so forth. They continued this process until they received consistent readings. This simple, one-time experience told them the exact time needed to evacuate the new product properly: a half-hour.
2) Determine Evacuation Process as Earlier as Possible
Just like the appliance manufacturer mentioned above, you should test the evacuation process as part of prototype development. Forget about computer modeling, that can take weeks. A couple of days of old-fashioned trial and error will determine the best refrigerant evacuation process for you.
3) Do Not Compensate with a Larger Vacuum Pump
When companies underestimate the time needed to evacuate, they often try to solve the problem by using a larger vacuum pump. But this does not work either. Basic engineering principles say that given the size of the pipe, there is a finite capacity for the amount of air and moisture that can travel through the pipe at the same time. If the vacuum pump you are replacing is already pulling out at the maximum rate, a larger vacuum pump will not make a difference.
One automotive manufacturer almost made this mistake. They originally thought a larger pump would decrease the time to evacuate. Instead, they decided to modify their refrigeration evacuation process. Before, they only attached the vacuum pump to the high-pressure side of the air conditioning system. Now, a vacuum pump is attached to both the high-pressure and low-pressure sides. This reduced the time required to evacuate by 20 percent and saved them unnecessary costs. The second tooling system was only $2,000 compared to the $6,000 required for a larger pump.
4) Avoid a “Sloshed” Reading
Air works in a refrigeration system much like liquid sloshing in a bottle turned on its side. After the evacuation, the air will slosh back and forth before leveling out. If you rush the isolation time—the time when you close the valve between the vacuum pump and the refrigeration system and wait for the air pressure to rise—you may end up reading the air as its sloshes, causing a false reading.
One auto manufacturer simply increased its isolation time by one second. That one second was enough time for the sensor to accurately read the pressure. This one second resulted in a 40 percent decrease in false positives/negatives.
Bottom Line
A fast and efficient refrigerant system evacuation process is possible. The key is to test your product prototypes before they reach the production line and determine how long each step should take. A little due diligence can prevent unnecessary costs and headaches.